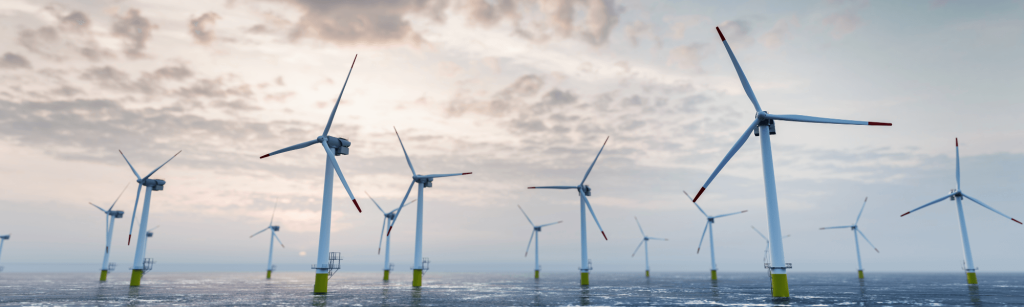
Even though offshore energy is still a relatively young field, offshore wind farms are becoming an increasingly attractive investment around the globe. The conditions for building wind parks in the sea are much more favorable than on land – the areas in the sea are large, and no mountains or settlements could complicate the construction.
RNDV provides offshore services such as the production of offshore metal structures and electrical installation. We invite you to deepen your knowledge and get acquainted with five interesting facts about offshore wind farms, their operation, and construction:
- Building a wind farm takes 6-12 years
The total time to install an offshore wind farm can vary depending on the scale of the project, location, and available resources. Still, building the park from planning to operation usually takes between 6 and 12 years.
Typically, the construction process of a wind farm is divided into three phases: design, pre-construction phase, and installation. The first stage, which consists of project development, development, and planning, can last 3 to 5 years. Subsequently, about 1-3 years are allocated to the pre-construction phase, during which the necessary contracts and other legal requirements are identified. Finally, the construction phase can take 2-4 years before the wind farm is ready for operation.
- 80 wind turbines help reduce CO2 emissions by as much as 80,000 tons
To better understand the efficiency of wind turbines, let’s consider the numbers. Each wind farm varies in size and power, but on average, one wind turbine can generate up to 30 000 kWh annually or more than 11 Millions kWh per year.
Wind farms help reduce energy dependence on fossil fuels, allow savings, and reduce the total amount of CO2 gas emitted into the environment. 80 wind turbines help reduce CO2 emissions by as much as 80,000 tons.
- The transformer platform can weigh up to 3000 tons
Each offshore wind farm has substations (transformer platforms) that collect and transform the produced electricity and prepare it for transmission to the shore. These stations help ensure that as little energy as possible is lost when supplying electricity over long distances.
Substations are installed offshore where extreme weather conditions such as strong winds or waves are common, so they are designed to withstand the harsh marine environment for years. The station itself, without installation at sea, can weight from 200 tons, and the installed and functioning station can weigh up to 3,000 tons.
- Wind turbines can last more than 30 years
Building wind turbines is a long-term investment into a cleaner future. Wind parks currently being built are expected to operate for at least 25-30 years. With proper maintenance and operation of the equipment, wind turbines can be successfully used even longer.
As a result, offshore wind farm structures are manufactured and installed with particular responsibility – wind turbines must withstand sea storms and waves and resist sea salinity and corrosion. At the end of the park’s operational period, all structures are dismantled, cut, and delivered to the scrap metal purchase point.
- The payback period of the wind turbine is 6 years
When choosing to invest in the construction of wind farms, it is worth considering the turbines’ positive environmental impact and payback figures. The wind turbine becomes climate neutral – i.e., the green energy generated offsets the amount of energy used to produce it – after about 4-7 months of operation.
The payback period for the wind turbine is currently six years. After six years of operation, the installed wind turbine generates profit, reaching 50 to 80 thousand EUR per year. The wind farm, which consists of 80 turbines, generates up to 6.5 million EUR annually.