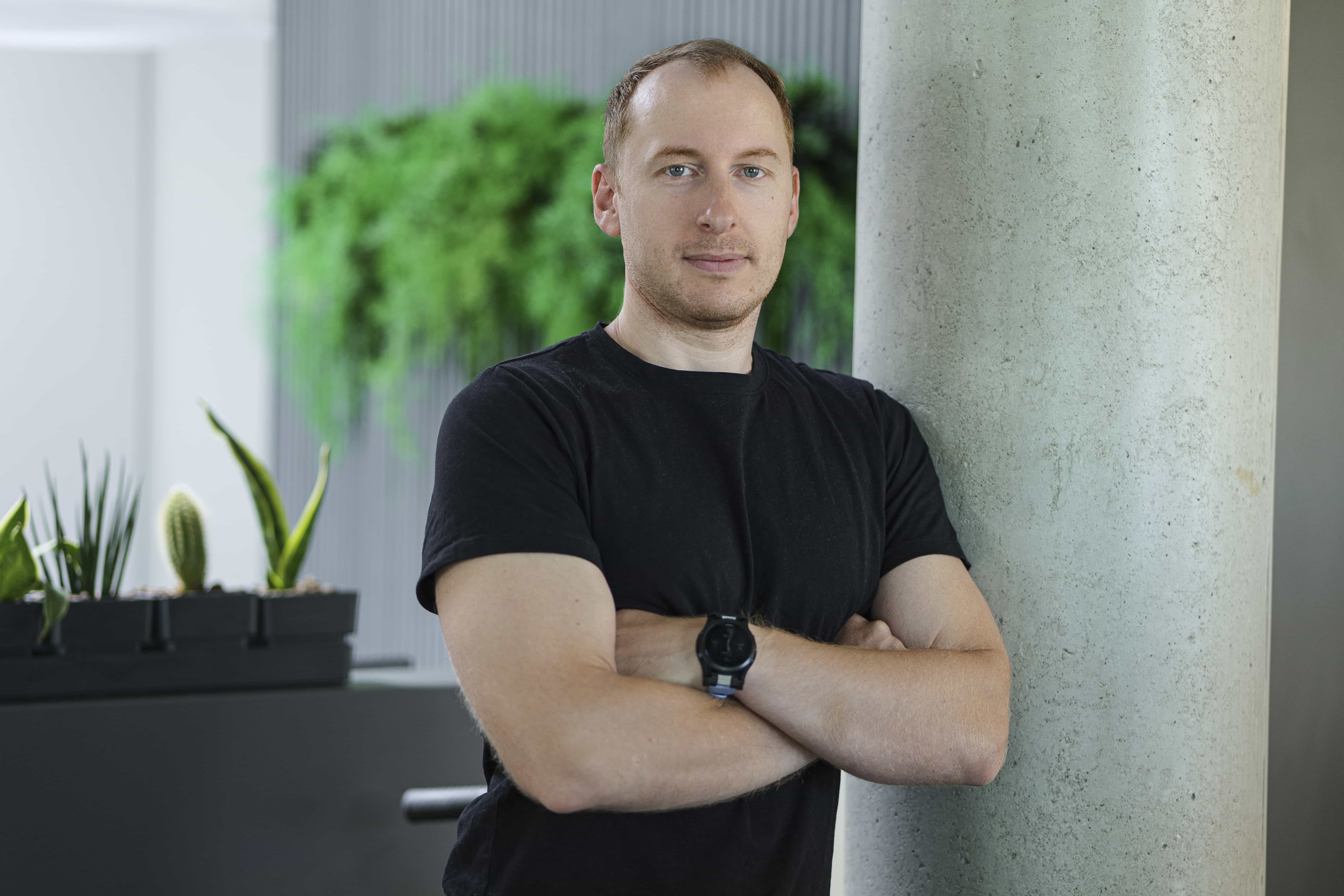
In our previous blogpost, RNDV Chief Project Officer Giedrius Grėbliūnas explored the complexities of construction productivity and the persistent challenges that limit its progress. Now, it’s time to dig deeper into one of the biggest barriers: waste.
Most of you are probably familiar with the term “waste” in production. These are the activities that occur during a project but do not add value. They can range from walking, searching for information, correcting defects, or even redoing work. In manufacturing, tremendous progress has been made to eliminate waste, driving efficiency gains up to eight times higher than in construction. How? By minimizing waste to just 12 percent of the production time!
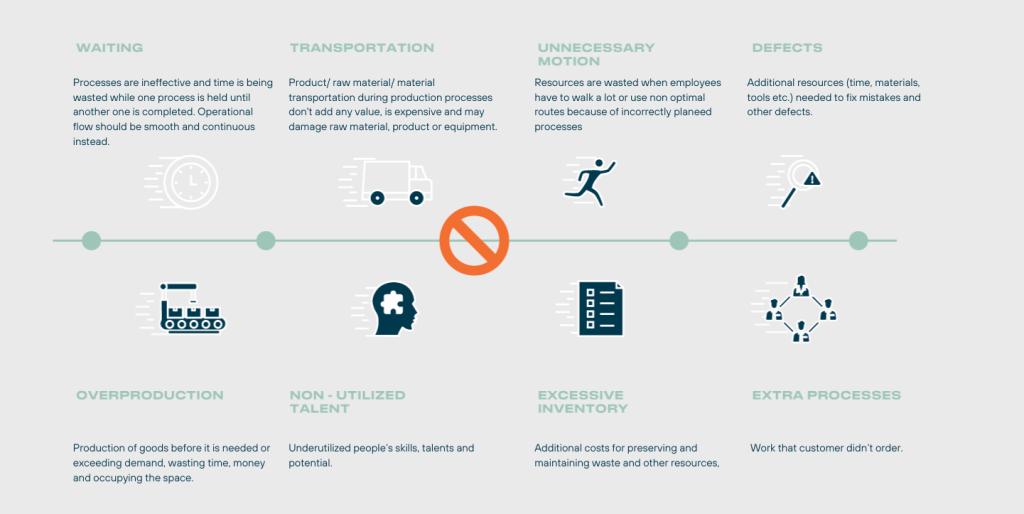
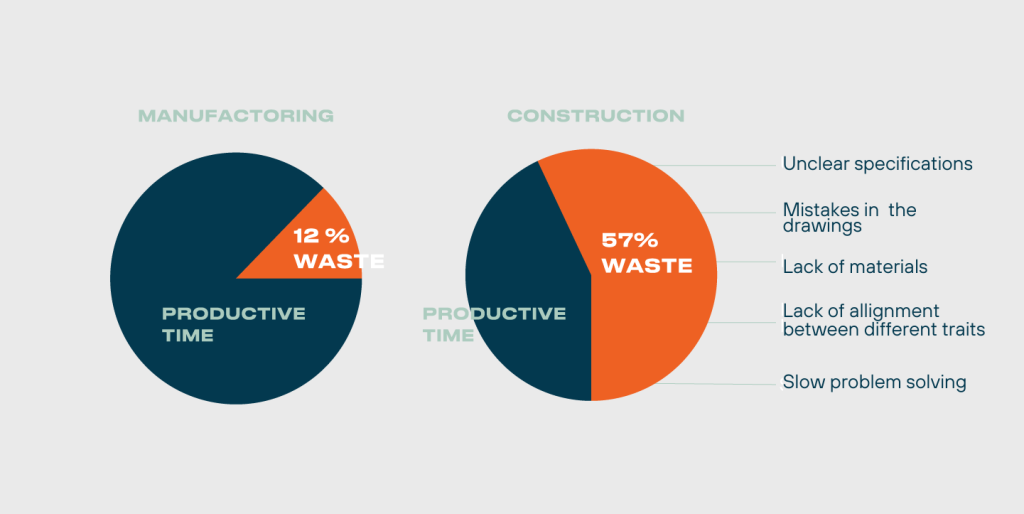
The Reality of Construction Wastes
Unfortunately, in construction, the story is different, marks Giedrius Grėbliūnas: “Wastes typically consume 57 percent of a project’s time. To put this into perspective: in a standard 10-hour workday, almost 6 hours are spent on activities that don’t contribute to the final product.”
These activities include:
- Searching for information due to unclear specifications.
- Time wasted fixing errors in drawings or waiting for answers.
- Frequent mobilization and demobilization, caused by having to move between different areas instead of completing work in one spot.
- Misalignment between different trades working on site, causing delays and confusion.
- Slow problem solving, leaving unfinished tasks that need to be revisited later.
In short, construction teams are often forced to spend valuable time on tasks that don’t directly contribute to the build, severely affecting overall productivity.
What Can Be Done?
It’s crucial to understand that the value added by each worker is generally fixed—there’s only so much a person can do in a day. Therefore, increasing efficiency isn’t about asking workers to move or install things faster. Instead, it’s about removing waste.
“By eliminating waste, we can free up time and redirect that effort into value-adding activities such as installing more units, pulling more meters, or painting more square meters. This transformation is key to boosting productivity,” says RNDV Chief Project Officer.
Visualizing the Impact of Waste Removal
Below, we offer a visual representation that highlights just how impactful eliminating waste can be. In RNDV’s own projects, we’ve seen firsthand that reducing obstacles for workers can cut the time required to complete a task by half when compared to traditional construction flows, where waste is prevalent.
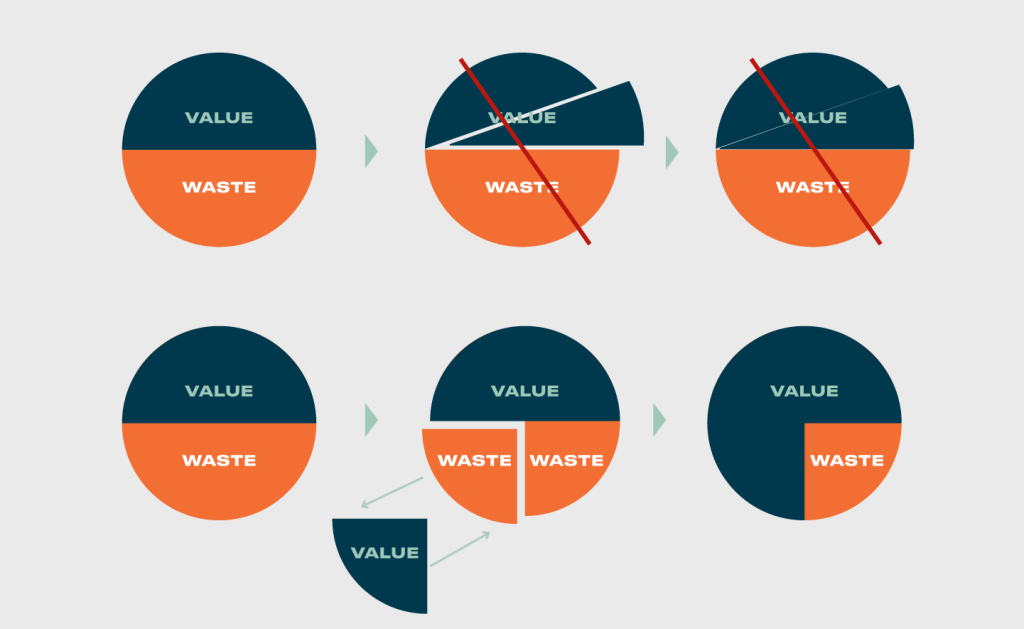
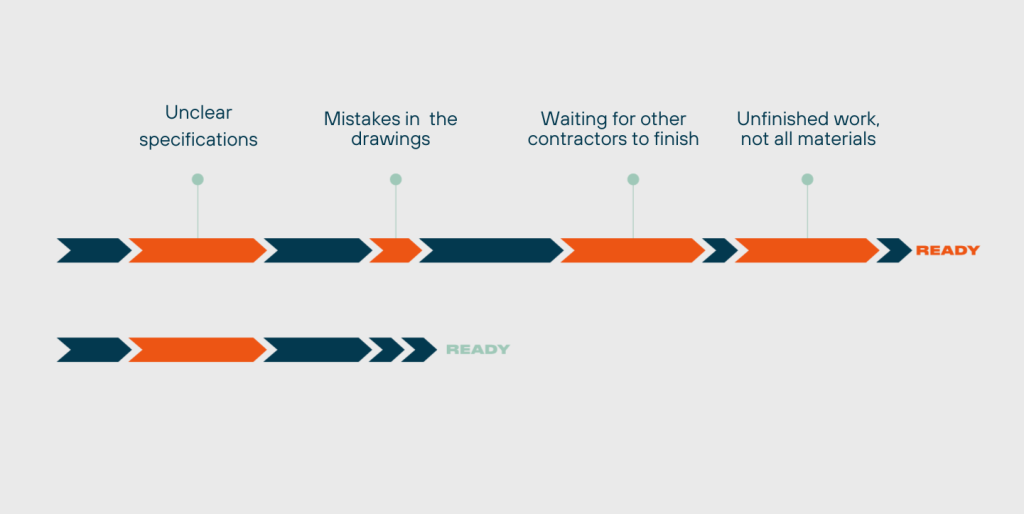
RNDV’s Approach: Measuring and Improving Efficiency
“At RNDV, we actively measure our efficiency through practices like Gemba walks, where we analyze real-time operations on site. From these observations, we’ve confirmed that removing waste—whether it’s unnecessary steps, delays, or miscommunication—dramatically speeds up project completion,” Giedrius Grėbliūnas shares his insights.
But, and this is important: such improvements only happen when all parties involved in the project collaborate closely. Solving issues upfront, aligning work across trades, and keeping the site conditions optimal are critical to making sure every worker can perform their job without unnecessary interruptions.
Conclusion
The construction industry has long lagged behind in productivity gains compared to manufacturing, but it doesn’t have to remain this way. By focusing on eliminating waste, we can unlock the potential to significantly boost efficiency on every project.
In the next post, Giedrius Grėbliūnas will explore how technologies and Lean methodologies can further help us improve processes and cut down on waste in construction. Stay tuned!